Gestione delle aree di contatto tra stampo e fuso: effetto di trasferimento di calore termico
Durante il riempimento dello stampo, nello stampaggio ad iniezione, a causa della resistenza termica di contatto tra stampo e materiale fuso, la temperatura dell'interfaccia intornoallo stampo-fuso (Tmt) è generalmente superiore alla temperatura impostata nello stampo (TMB).
La differenza tra Tmb e Tmt dipende dalle proprietà termiche superficiali del metall, caratteristiche del materiale fuso, e sulle condizioni di processo utilizzate.
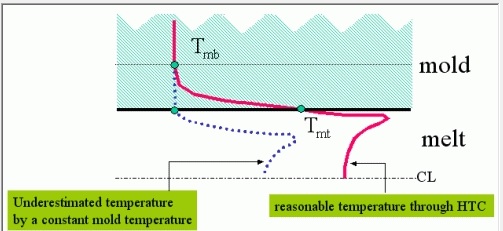
Il problema temperatura fissa per la definizione delle condizioni al contorno
In situazioni “standard”, la Tmt non può essere molto diversa da Tmb. Ciò significa che è possibile applicare il Tmb per rappresentare la Tmt direttamente nella simulazione CAE stampaggio.
Tuttavia, per i casi con parti a parete sottile, riempimenti ad alta velocità o con viscosità fortemente dipendente dalla temperatura, ecc.ecc. l'uso del solo Tmb tende a tradursi in temperatura più bassa, di quello che in realtà è, nella zona di interfaccia stampo-fuso, che porta quindi a previsione pressione di iniezione superiore a quello che invece i rilievi fisici/sperimentali riportano.
La necessità di utilizzo del coefficiente composto nella funzione di trasferimento del calore (HTC).
Spesso è conveniente lavorare con il coefficiente di scambio termico (HTC), che è definito da un'espressione analoga alla legge di raffreddamento di Newton.
q = hc (Tmt-TMB)
Il coefficiente di trasmissione del calore (hc) tra la base e la parte dello stampo dipende da materiali, temperatura e condizioni di processo. In genere, la gamma di hc è 1000-25000 (W / m ^ 2.K).
Quando si utilizza un hc superiore, il flusso di calore trasferimento “q” è maggiore.
La temperatura Tmt sarà più vicina alla temperatura stampo base Tmb.
Al contrario, quando si usa un valore hc più basso, la temperatura Tmt sarà molto superiore alla temperatura stampo base Tmb; da questo la necessità di effettuare un controllo più sofisticato del fenomeno.
Le nuove funzionalità introdotte, tra cui quella del poter tener conto del Numero di Nusselt, aumentano il livello di affidabilità dei risultati della simulazione con Moldex3D.